ACCY112 Lecture Notes - Lecture 10: Finished Good, Financial Accounting, Financial Statement
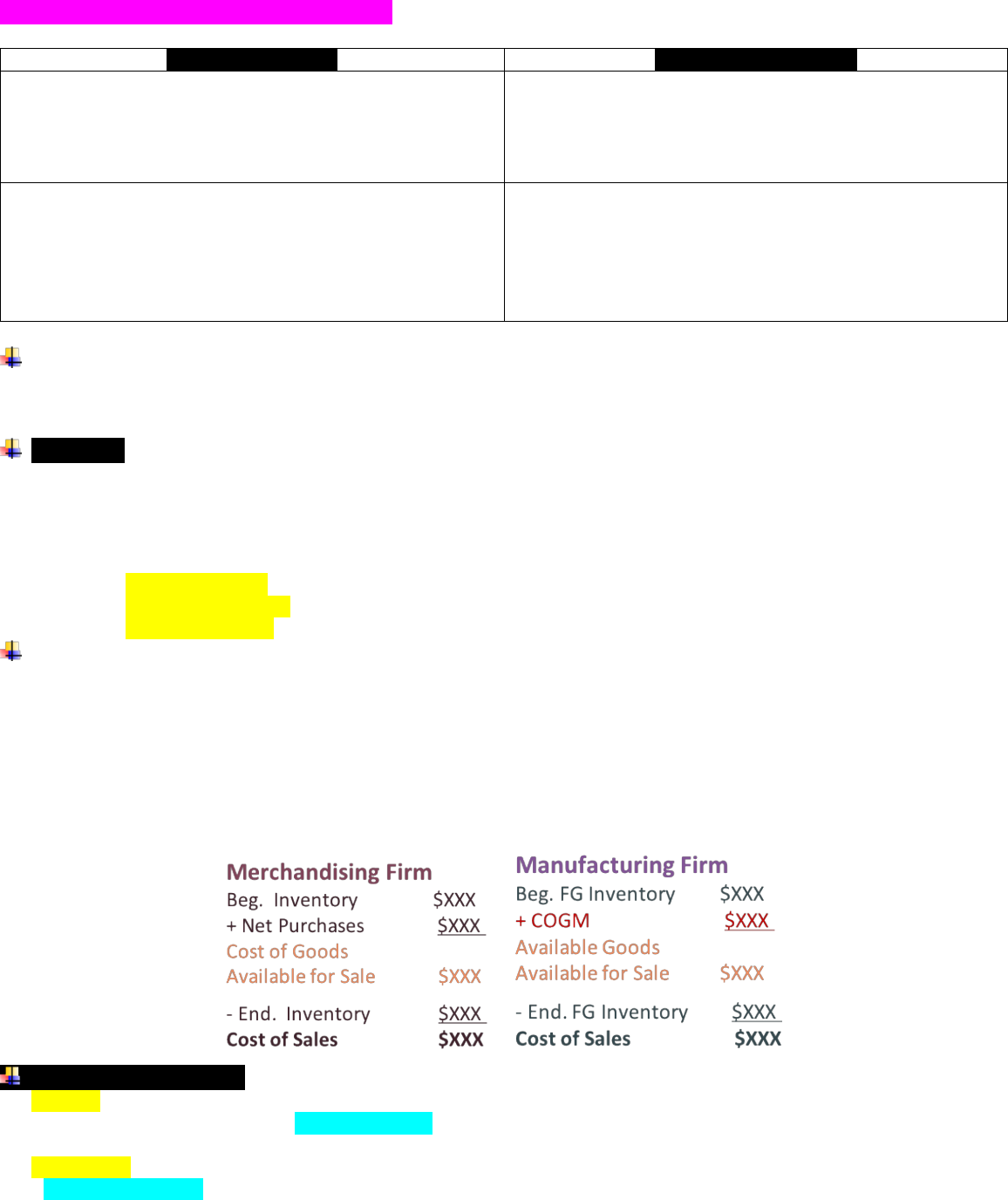
ACCOUNTING FOR MANUFACTURING
Financial accounting
Management accounting
Concerned with reporting financial information to users
external to an entity in order to help them to make sound
economic decisions about the entity’s performance and
financial position.
Concerned with reporting financial and other information to
all level of management in an organisation to enable them to
carry out their planning, controlling and decision-making
responsibilities
• External focus
• Reporting information
- Performance
- Position
• Financing and investing
• Compliance
• Internal focus
- Planning
- Controlling
- Decision-making
• Cost behaviour
• Budgeting
Cost concept in different sectors
1. Service company: provides intangible services, rather than tangible products.
2. Retail company: resells products previously bought from suppliers.
3. Manufacturing company: use labour, plant and equipment to convert raw materials into finished products.
Inventories- manufacturing and non-manufacturing:
1. Service entities: have no significant inventory
2. Retail entities:
- Buy finished goods for resale
- Generally have one inventory control account
4. Manufacturing entities:
- Raw materials
- Work in progress
- Finished goods
Comparing retailing and manufacturing accounting
❖ Type of activity:
- Manufacturer converts raw materials and components into finished products
- Retailer buys products already finished and sell them to customers
❖ Complexity:
- Manufacturing has additional types of expenditure: manufacturing cost.
- Manufacturing has additional types of inventory: raw materials, work in progress and finished goods.
❖ Report:
- Manufacturing has additional statement, the Manufacturing Statement (cost of goods manufactured).
COSTS AND EXPENSES
◼ Cost
- Economic sacrifice of resources made in exchange for a product or service
(Example: purchased inventory)
◼ Expense
- Consumption or loss of resources
(Example: Used inventory)
◼ Some of the reasons managers need to know about the costs of manufacturing include:
o Inventory Valuation
o Profit Determination
o Management Decision-Making Applications
find more resources at oneclass.com
find more resources at oneclass.com
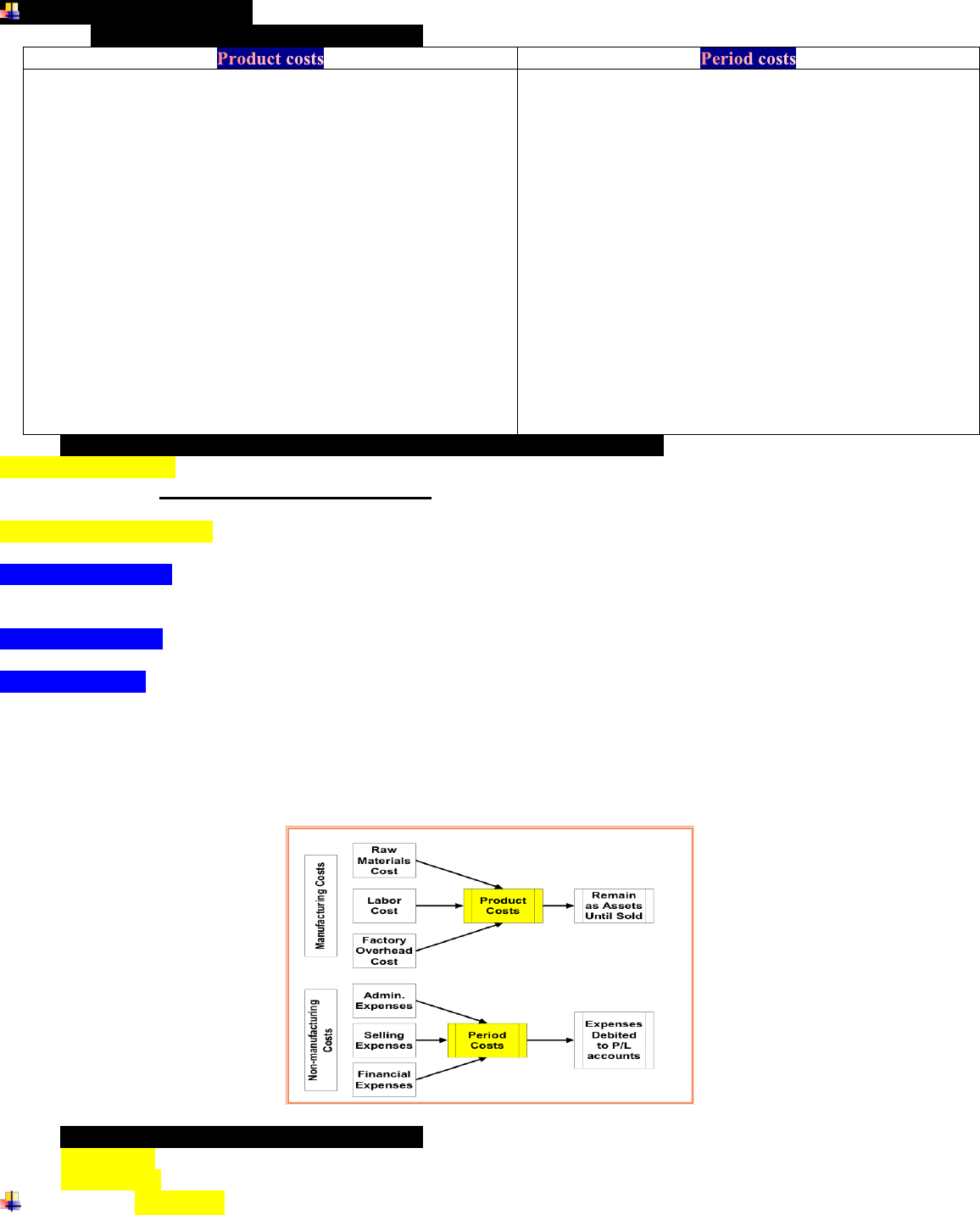
COST CLASSIFICATION:
1. Time frame: Product costs vs Period costs
- Are costs incurred in the factory
- factory overhead costs may include electricity, indirect
supervision, depreciation of equipment. These must be
incurred in the factory.
- Three types of Product Costs:
- Material Costs
- Labour Costs
- Overhead Costs
- Product costs are the equivalent to what merchandise
costs for a retailer.
- As with a retailer, if products are unsold, these costs are
recorded in the balance sheet and are capitalised (also
called unexpired costs).
- That is why product costs also known as inventoriable
costs.
- Become expense of the current period when product is
sold.
o Period costs are all costs in the statement of financial
performance.
▪ when the product made is sold, the costs are
transferred from the balance sheet where they
appear as inventory of Work In Process or
Finished Goods, to the income statement.
• These product costs then become
period or expired cost.
▪ Recorded as expenses of the accounting
period in which they are incurred. For
example, selling and administrative
expenses
2. Management function: manufacturing costs vs non-manufacturing costs
Manufacturing Costs:
✓ They are the costs to produce tangible products intended for sale. All manufacturing costs treated as the cost of the
product until the product is sold
Non-manufacturing Costs:
✓ They are the costs incurred in a manufacturing company other than to produce tangible products intended for sale.
Direct Material Costs
o All raw materials or parts that physically make up the product (ex: paint, plastic, motors... )
_which are considered to have a direct relationship to form the finished products.
Direct Labour Costs
o Costs of workers who apply their skills directly to the making of the product.
Factory Overhead
o All costs (other than Direct Material and Direct Labour) that are associated with the manufacture of the product.
o Examples:
• Cost of indirect materials (factory supplies, Indirect Factory Labour, Depreciation of machinery and factory,
• Factory utilities (electricity, gas, water bills cua factory only)
• Factory insurance
• Factory rent, depreciation, maintenance
3. Traceability: Direct costs vs indirect costs
◼ Direct costs: are those costs that can be specifically traced to the cost object.
◼ Indirect costs: are costs that cannot be specifically traced to the cost object.
Two Types of Direct costs:
• Direct Material Costs: Cost of raw materials directly traceable to the finished product
find more resources at oneclass.com
find more resources at oneclass.com
Document Summary
Concerned with reporting financial information to users external to an entity in order to help them to make sound economic decisions about the entity"s performance and financial position. Concerned with reporting financial and other information to all level of management in an organisation to enable them to carry out their planning, controlling and decision-making responsibilities: external focus, reporting information. Decision-making: cost behaviour, budgeting, service company: provides intangible services, rather than tangible products, retail company: resells products previously bought from suppliers, manufacturing company: use labour, plant and equipment to convert raw materials into finished products. Inventories- manufacturing and non-manufacturing: service entities: have no significant inventory, retail entities: Generally have one inventory control account: manufacturing entities: Manufacturer converts raw materials and components into finished products. Retailer buys products already finished and sell them to customers. Manufacturing has additional types of expenditure: manufacturing cost. Manufacturing has additional types of inventory: raw materials, work in progress and finished goods.