SCM 301 Chapter Notes - Chapter 12: Anxiety, Purchasing Manager, Material Requirements Planning
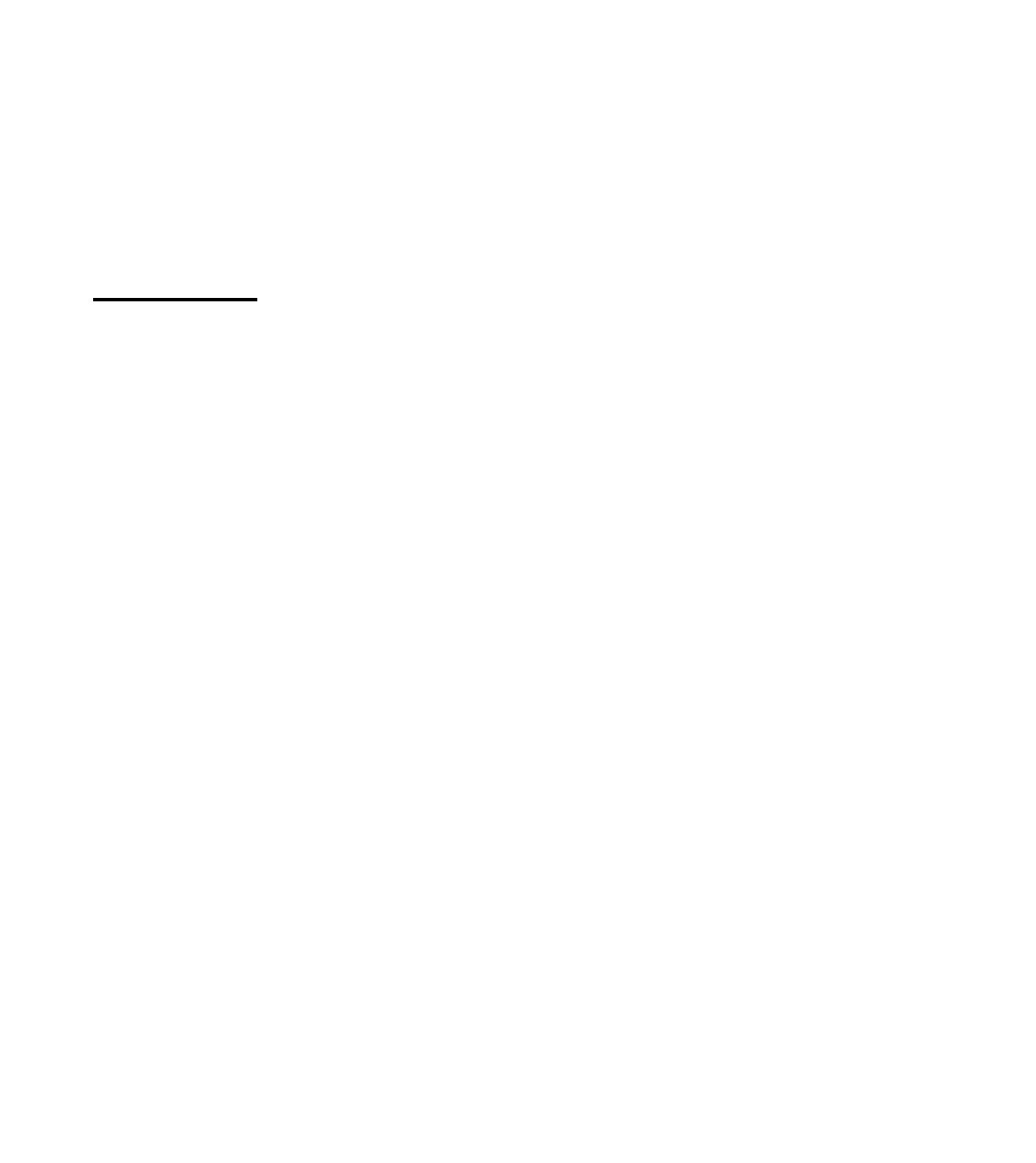
Introduction
Planning and Control: a set of tactical and execution level
business activities that include master scheduling,
material requirements planning, and some form of
production activity control and vendor order
management
Planning and Control begins where sales and
operations planning (S&OP) ends
○
Planning and Control Steps
Master Scheduling: determines when specific
products will be made, when specific customer
orders will be filled, and what
products/capacities are still available to meet
new demand
Available to Promise
□
§
Material Requirements Planning (MRP):
translates master schedule for final production
into detailed material requirements
Calculate timing and quantities of material
orders needed to support the master
schedule
□
§
Production Activity Control (PAC) & Vendor
Order Management
PAC: assures that in-house manufacturing
takes place according to plan; also helps
manufacturing managers identify potential
problems and take corrective actions
□
Vendor Order Management: assures that
materials ordered from supply chain
partners are received when needed; also
helps purchasing managers identify
potential problems and take corrective
action
□
§
○
•
12.1 Master Scheduling
Master Scheduling: a detailing planning process that
tracks production outputs and matches this output to
actual customer orders
The Link between the S&OP and the Master
Scheduling: inventory levels in both should be equal,
while demand and production are similar but may
not be equal
○
Benefits: allows managers to take corrective action
when needed,
○
•
The Master Schedule Record
Track key pieces of information:
Forecasted demand
§
Booked orders
§
Projected inventory levels
§
Production quantities
§
Units still available to meet customer needs
(available to promise)
§
○
Forecasted Demand: in context of master schedule, a
company's best estimate of the demand in any
period
○
Booked Orders: in context of master schedule,
confirmed demand for production
○
Master Production Schedule (MPS): shows how many
products will be finished and available for sale at the
beginning of each week
○
Projected Ending Inventory: best estimate of what
inventory levels will look like at the end of each week
based on current information
𝐸𝐼#=𝐸𝐼#%& +𝑀𝑃𝑆#−max(𝐹#,𝑂𝐵#)
EIt= endig inventory in time period t
MPSt= master production schedule quantity
available in period t
Ft= forecasted demand for time period t
Obt= orders booked for time period t
○
Available to Promise (ATP): field in the master
schedule record that indicates the number of units
that are available for sale each week, given those
that have already been promised to customers
Think of it as what's still available that we
haven't already committed to customers
§
First week:
𝐴𝑇𝑃#=𝐸𝐼#%& +𝑀𝑃𝑆#−7𝑂𝐵8
9%&
8:#
ATPt= available to promise in week t
Eit-1= ending inventory in week t-1
MPSt= master production schedule
quantity in week t
∑𝑂𝐵8
9%&
8:# <= sum of all orders booked
from week t until the next positive
MPS quantity is due
§
Any subsequent week in which MPS>0:
𝐴𝑇𝑃#=𝑀𝑃𝑆#−7𝑂𝐵8
9%&
8:#
**KEY HOLDS CONSTANT AS ABOVE EQUATION**
§
○
•
Planning Horizon: amount of time the master schedule
record or MRP record extends into the future. In general,
the longer the production and supplier lead times, the
longer the planning horizon must be
•
Time Fences: how long it will take to get all components
together to make product
Weeks go from Frozen, moderately firm, to flexible
○
•
12.2 Material Requirements Planning
Rough-Cut Capacity Planning: capacity technique that
uses the master production schedule to monitor key
resource requirements
•
Material Requirements Planning (MRP): translates master
schedule into planned orders for actual parts and
components needed to produce the items in the master
schedule
•
Dependent Demand Inventory: inventory items whose
demand levels are tied directly to the production of
another item
•
MRP is based on three related concepts:
The bill of material (BOM)
○
Backward Scheduling
○
Explosion of the bill of materials
○
•
Bill of Material (BOM): a listing of all of the subassemblies,
intermediates, parts, and raw materials that go into a
parent assembly showing the quantity of each required to
make an assembly
Parent is the finished product
○
Child are the components
○
Product Structure Tree: a record of graphical
rendering that shows how the components in the
BOM are put together to make the level 0 item
○
Planning Lead Time: in MRP context, the time from
when a component is ordered until it arrives and is
ready to use
○
Backward Scheduling (Exploding the BOM)
Process of working backward from the master
production schedule for a level 0 item to
determine the quantity and timing of orders for
the various subassemblies and components
§
Underlying logic used by MRP
§
○
•
The MRP Record
Gross Requirements: total demand each week
○
Scheduled Receipts: units already ordered and
scheduled to come in
○
Projected Ending Inventory
○
Net Requirements: new orders that needed to be
placed
𝑁𝑅#=𝑚𝑎𝑥𝑖𝑚𝑢𝑚(0;𝐺𝑅#−𝐸𝐼#%& −𝑆𝑅#)
NRt= net requirement in time period t
GRt= gross requirement for time period t
Eit-1= ending inventory from time period t-1
SRt= scheduled receipts in time period t
○
Planned Receipts: new orders
○
Planned Order Releases: orders we know will be
coming
○
•
MRP Dynamics
Supports replanning
○
Time Fence
○
Pegging
○
That a manager CAN react to changes, doesn’t mean
he/she should
○
•
Lot Sizing Techniques
Lot for Lot : minimum order quantity=1, order
whatever is needed
○
EOQ:
○
Minimum Quantity: order in multiples of the quantity
given
○
•
MRP Advantages
MRP is directly tied to the master production
schedule and indicates the exact timing and quantity
of orders for all components
○
MRP allows managers to trace every order for lower-
level items through all the levels of the BOM, up to
the Master Production Schedule
○
MRP tells a firm and its suppliers precisely what
needs to be made when
○
•
Special Considerations in MRP
Requires organizational discipline, MRP provides little
benefit to those who do not understand and exploit
the system
○
MRP must have accurate information, key data
includes master production scheduling, the BOM,
inventory levels, and planning lead times
○
MRP systems accommodate uncertainty about
possibility of variable lead times, shipment quantities
and quality levels, and quantity changes in the
master production schedule
○
MRP Nervousness: term used to refer to the
observation that any change, even a small one, in the
requirements for items at the top of the bill of
materials can have drastic effects on items further
down the bill of materials
○
•
12.4 Synchronizing Planning and Control Across the Supply
Chain
Distribution Requirements Planning: time-phased
planning approach similar to MRP that uses planned
orders at the point of demand to determine forecasted
demand at the source level (often a plant)
•
Chapter 12: Production
Wednesday, April 11, 2018
1:18 PM
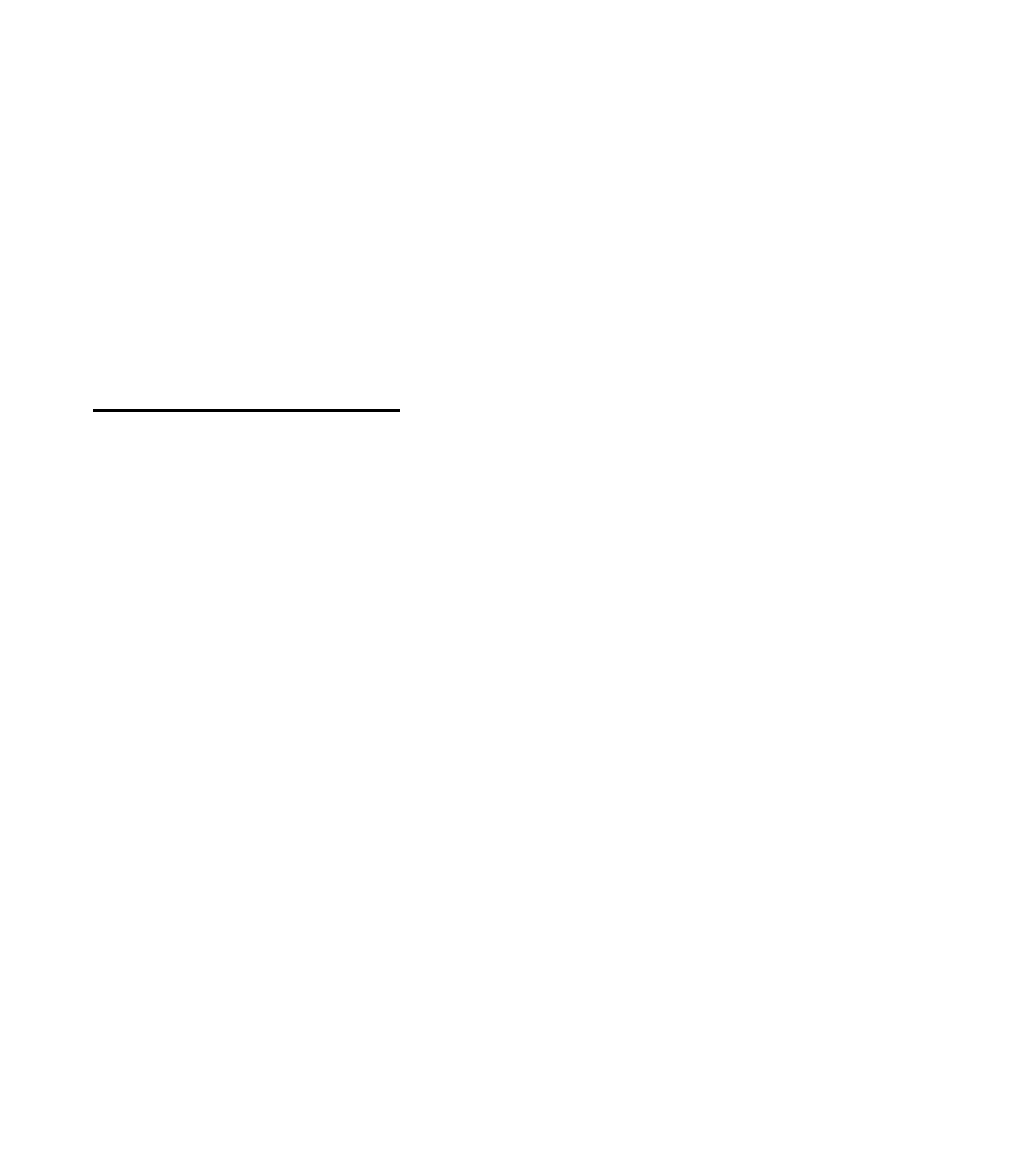
Introduction
Planning and Control: a set of tactical and execution level
business activities that include master scheduling,
material requirements planning, and some form of
production activity control and vendor order
management
Planning and Control begins where sales and
operations planning (S&OP) ends
○
Planning and Control Steps
Master Scheduling: determines when specific
products will be made, when specific customer
orders will be filled, and what
products/capacities are still available to meet
new demand
Available to Promise□
§
Material Requirements Planning (MRP):
translates master schedule for final production
into detailed material requirements
Calculate timing and quantities of material
orders needed to support the master
schedule
□
§
Production Activity Control (PAC) & Vendor
Order Management
PAC: assures that in-house manufacturing
takes place according to plan; also helps
manufacturing managers identify potential
problems and take corrective actions
□
Vendor Order Management: assures that
materials ordered from supply chain
partners are received when needed; also
helps purchasing managers identify
potential problems and take corrective
action
□
§
○
•
12.1 Master Scheduling
Master Scheduling: a detailing planning process that
tracks production outputs and matches this output to
actual customer orders
The Link between the S&OP and the Master
Scheduling: inventory levels in both should be equal,
while demand and production are similar but may
not be equal
○
Benefits: allows managers to take corrective action
when needed,
○
•
The Master Schedule Record
Track key pieces of information:
Forecasted demand
§
Booked orders
§
Projected inventory levels
§
Production quantities
§
Units still available to meet customer needs
(available to promise)
§
○
Forecasted Demand: in context of master schedule, a
company's best estimate of the demand in any
period
○
Booked Orders: in context of master schedule,
confirmed demand for production
○
Master Production Schedule (MPS): shows how many
products will be finished and available for sale at the
beginning of each week
○
Projected Ending Inventory: best estimate of what
inventory levels will look like at the end of each week
based on current information
𝐸𝐼#=𝐸𝐼#%& +𝑀𝑃𝑆#−max(𝐹#,𝑂𝐵#)
EIt= endig inventory in time period t
MPSt= master production schedule quantity
available in period t
Ft= forecasted demand for time period t
Obt= orders booked for time period t
○
Available to Promise (ATP): field in the master
schedule record that indicates the number of units
that are available for sale each week, given those
that have already been promised to customers
Think of it as what's still available that we
haven't already committed to customers
§
First week:
𝐴𝑇𝑃#=𝐸𝐼#%& +𝑀𝑃𝑆#−7𝑂𝐵8
9%&
8:#
ATPt= available to promise in week t
Eit-1= ending inventory in week t-1
MPSt= master production schedule
quantity in week t
∑𝑂𝐵8
9%&
8:# <= sum of all orders booked
from week t until the next positive
MPS quantity is due
§
Any subsequent week in which MPS>0:
𝐴𝑇𝑃#=𝑀𝑃𝑆#−7𝑂𝐵8
9%&
8:#
**KEY HOLDS CONSTANT AS ABOVE EQUATION**
§
○
•
Planning Horizon: amount of time the master schedule
record or MRP record extends into the future. In general,
the longer the production and supplier lead times, the
longer the planning horizon must be
•
Time Fences: how long it will take to get all components
together to make product
Weeks go from Frozen, moderately firm, to flexible
○
•
12.2 Material Requirements Planning
Rough-Cut Capacity Planning: capacity technique that
uses the master production schedule to monitor key
resource requirements
•
Material Requirements Planning (MRP): translates master
schedule into planned orders for actual parts and
components needed to produce the items in the master
schedule
•
Dependent Demand Inventory: inventory items whose
demand levels are tied directly to the production of
another item
•
MRP is based on three related concepts:
The bill of material (BOM)
○
Backward Scheduling
○
Explosion of the bill of materials
○
•
Bill of Material (BOM): a listing of all of the subassemblies,
intermediates, parts, and raw materials that go into a
parent assembly showing the quantity of each required to
make an assembly
Parent is the finished product
○
Child are the components
○
Product Structure Tree: a record of graphical
rendering that shows how the components in the
BOM are put together to make the level 0 item
○
Planning Lead Time: in MRP context, the time from
when a component is ordered until it arrives and is
ready to use
○
Backward Scheduling (Exploding the BOM)
Process of working backward from the master
production schedule for a level 0 item to
determine the quantity and timing of orders for
the various subassemblies and components
§
Underlying logic used by MRP
§
○
•
The MRP Record
Gross Requirements: total demand each week
○
Scheduled Receipts: units already ordered and
scheduled to come in
○
Projected Ending Inventory
○
Net Requirements: new orders that needed to be
placed
𝑁𝑅#=𝑚𝑎𝑥𝑖𝑚𝑢𝑚(0;𝐺𝑅#−𝐸𝐼#%& −𝑆𝑅#)
NRt= net requirement in time period t
GRt= gross requirement for time period t
Eit-1= ending inventory from time period t-1
SRt= scheduled receipts in time period t
○
Planned Receipts: new orders
○
Planned Order Releases: orders we know will be
coming
○
•
MRP Dynamics
Supports replanning
○
Time Fence
○
Pegging
○
That a manager CAN react to changes, doesn’t mean
he/she should
○
•
Lot Sizing Techniques
Lot for Lot : minimum order quantity=1, order
whatever is needed
○
EOQ:
○
Minimum Quantity: order in multiples of the quantity
given
○
•
MRP Advantages
MRP is directly tied to the master production
schedule and indicates the exact timing and quantity
of orders for all components
○
MRP allows managers to trace every order for lower-
level items through all the levels of the BOM, up to
the Master Production Schedule
○
MRP tells a firm and its suppliers precisely what
needs to be made when
○
•
Special Considerations in MRP
Requires organizational discipline, MRP provides little
benefit to those who do not understand and exploit
the system
○
MRP must have accurate information, key data
includes master production scheduling, the BOM,
inventory levels, and planning lead times
○
MRP systems accommodate uncertainty about
possibility of variable lead times, shipment quantities
and quality levels, and quantity changes in the
master production schedule
○
MRP Nervousness: term used to refer to the
observation that any change, even a small one, in the
requirements for items at the top of the bill of
materials can have drastic effects on items further
down the bill of materials
○
•
12.4 Synchronizing Planning and Control Across the Supply
Chain
Distribution Requirements Planning: time-phased
planning approach similar to MRP that uses planned
orders at the point of demand to determine forecasted
demand at the source level (often a plant)
•
Chapter 12: Production
Wednesday, April 11, 2018 1:18 PM
Document Summary
Planning and control: a set of tactical and execution level business activities that include master scheduling, material requirements planning, and some form of production activity control and vendor order management. Planning and control begins where sales and operations planning (s&op) ends. Master scheduling: determines when specific products will be made, when specific customer orders will be filled, and what products/capacities are still available to meet new demand. Material requirements planning (mrp): translates master schedule for final production into detailed material requirements. Calculate timing and quantities of material orders needed to support the master schedule. Pac: assures that in-house manufacturing takes place according to plan; also helps manufacturing managers identify potential problems and take corrective actions. Vendor order management: assures that materials ordered from supply chain partners are received when needed; also helps purchasing managers identify potential problems and take corrective action. Master scheduling: a detailing planning process that tracks production outputs and matches this output to actual customer orders.