FNEC-2600 Study Guide - Midterm Guide: Cost Driver, Direct Labor Cost, Contribution Margin
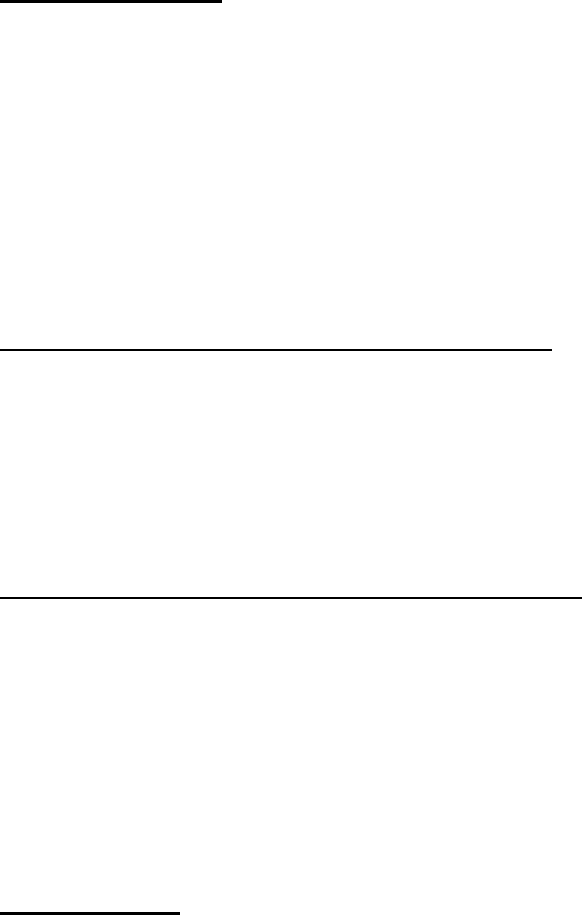
FNEC 2600 – Test 2 Review
Multiple Choice Topics: (13 Questions, 26 Points)
1. Understanding ABC (when it should be considered, results,
drawbacks, etc.)
When to Switch to ABC
1. Non-unit level activities constitute a significant portion of total overhead costs.
2. When a product’s consumption ratio for non-unit level activities varies significantly from the
consumption ratios of unit-level activities.
3. Product lines differ greatly in volume and complexity
4. Product lines are numerous, diverse, and require differing degrees of support
services.
5. The manufacturing process or product line has changed significantly.
6. Production or marketing mgrs are ignoring data provided by the existing system.
Typical Results of ABC vs. Traditional Allocation Methods
Overhead cost allocations generally shift from the high-volume products to the low-volume products.
There were two reasons for this result:
1. Low-volume products often require special handling, more setups, and more
inspections.
2. A traditional overhead allocation such as direct labor hours is usually a poor cost driver for
assigning overhead to low-volume products.
Why ABC is More Accurate than Traditional Costing Methods
1. ABC utilizes more cost pools (i.e. multiple drivers) to assign overhead costs to products.
Traditional systems use a single cost driver even though that driver may not be appropriate for all
overhead activities.
2. ABC leads to enhanced control over overhead costs. As overhead costs are traced to
activities, some indirect costs can be identified as direct costs.
3. ABC leads to better management decisions. More accurate product costing should contribute
to setting selling prices that help achieve desired profit levels. It also helps with
make/buy/discontinue decisions.
Limitations of ABC
1. ABC can be expensive. The software is more complex and it is costly to identify multiple
activities and apply numerous cost drivers. Cost/Benefit analyses must first be performed.
2. Some arbitrary allocations continue.
find more resources at oneclass.com
find more resources at oneclass.com
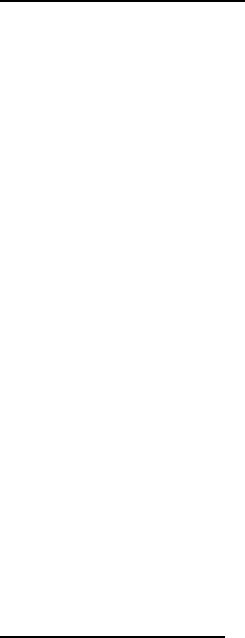
2. Basic understanding of ‘Costs of Quality’
Quality Cost Management
The idea is to increase customer demand while decreasing costs by focusing on the four Costs of
Quality. Costs of quality fall into two subcategories; 1) Control Activities and 2) Failure Activities.
Control Activities:
1. Prevention Costs – costs to ensure tasks are performed correctly the 1st
time and products & services meet customer requirements. Examples
include employee training, education of suppliers, preventive
maintenance.
2. Appraisal/Detection Costs – amounts spent on inspections, testing, and
sampling materials, WIP, & finished goods & services to remove low-quality
products & services from the system.
Failure Activities:
3. Internal Failure Costs – costs for scrap and rework incurred to dispose
of or fix defective products before they are shipped.
4. External Failure Costs – failure after the product has been delivered.
Examples include processing complaints, customer returns, warranty
claims, recalls, and product liability.
3. What takes place during process-value analysis
Process-Value Analysis – focus on cost reduction, not cost assignment
1. Driver Analysis: What causes activity costs; analyzing activity inputs (resources), activity
outputs, and output measures. The idea is to minimize the root cause of the activity cost
(example may be changing the plant layout to reduce the cost of moving materials).
2. Activity Analysis: Emphasizes determination of the value-added content of activities. Value-
added activities are required / necessary to stay in business. Nonvalue-added activities add no
value to the customer. Leads to:
a. Activity Elimination (nonvalue-added)
b. Activity Selection (competing activities)
c. Activity Reduction (time & resources)
d. Activity Sharing (example; sharing components increases efficiency)
3. Activity Performance Measurement: Assess performance in terms of:
a. Efficiency (do more with less)
b. Time (less time uses less resources)
Quality (do it right the first time)
4. Be familiar with the different cost types and cost behaviors
find more resources at oneclass.com
find more resources at oneclass.com
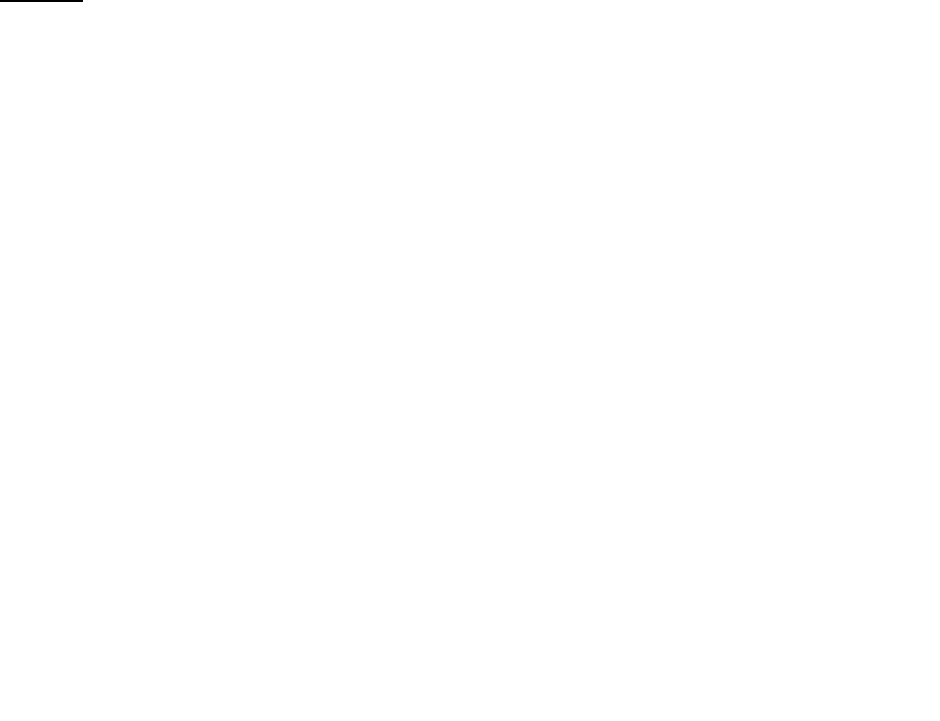
Fixed Cost – Total Cost remains constant as output changes. However, per unit cost has an indirect
relationship to changes in output.
Step Cost (Semi-Fixed) – A cost that remains constant (fixed) for an output range and then jumps when
a certain level of output is reached. It will then remain constant over that level until another level is
reached. These levels would all fall within the relevant range.
Variable Cost – Total Cost changes in direct proportion to changes in activity. On a per unit basis, the
cost remains constant.
Mixed Cost – contains characteristics of both a variable cost and a fixed cost.
Example: A lease agreement for a copier could be based on flat monthly fee of $200 (fixed) plus a
usage fee of 5 cents per copy (variable) when the total copies exceed 5,000 during a month.
5. Understand cost-volume-profit relationships (i.e. components
used to determine break-even, target profit, other what if
scenarios)
See below.
6. What creates operating leverage and the impact of operating
leverage on profits
Operating leverage is a measurement of the degree to which a firm or project incurs a combination of
fixed and variable costs. A business that makes sales providing a very high gross margin and fewer fixed
costs and variable costs has much leverage. A company with high operating leverage has a high
percentage of fixed costs to total costs, which means more units have to be sold to cover costs. A
company with low operating leverage has a high percentage of variable costs to total costs, which means
fewer units have to be sold to cover costs. In general, a higher operating leverage leads to lower profits.
Problems:
1. Breaking down a mixed cost (10 points): using the high-low
method (Chapter 3 type problem)
Based on a table of total costs and activity levels, determine the high and low activity levels.
find more resources at oneclass.com
find more resources at oneclass.com
Document Summary
Multiple choice topics: (13 questions, 26 points: understanding abc (when it should be considered, results, drawbacks, etc. ) Overhead cost allocations generally shift from the high-volume products to the low-volume products. Why abc is more accurate than traditional costing methods: abc utilizes more cost pools (i. e. multiple drivers) to assign overhead costs to products. Traditional systems use a single cost driver even though that driver may not be appropriate for all overhead activities: abc leads to enhanced control over overhead costs. As overhead costs are traced to activities, some indirect costs can be identified as direct costs: abc leads to better management decisions. More accurate product costing should contribute to setting selling prices that help achieve desired profit levels. Limitations of abc: abc can be expensive. The software is more complex and it is costly to identify multiple activities and apply numerous cost drivers. Cost/benefit analyses must first be performed: some arbitrary allocations continue, basic understanding of costs of quality".