ACC 406 Chapter Notes - Chapter 5: Income Statement, Cost Driver
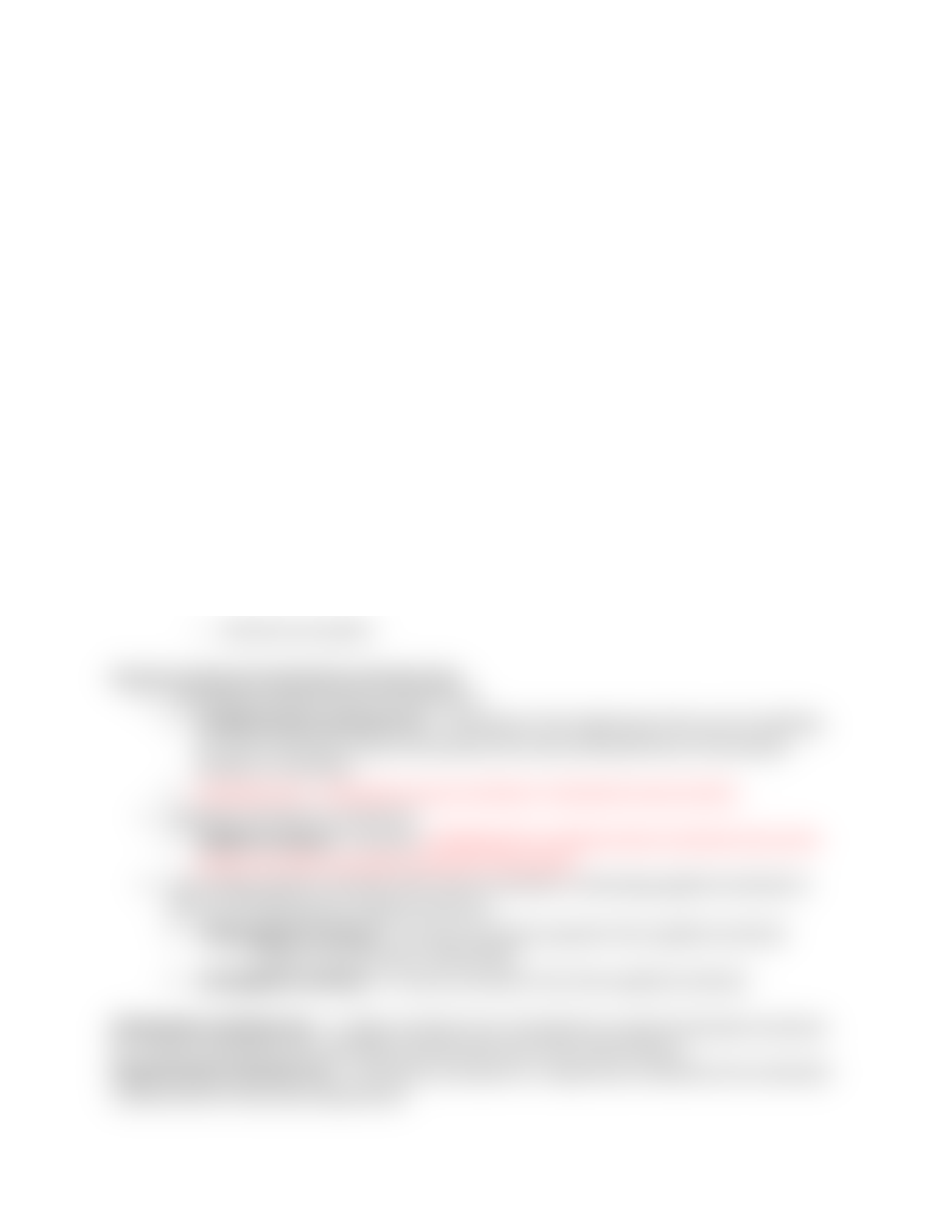
ACC – Chapter 5 – Job Order Costing
Firms producing unique products or services require a job-order accounting system
Firms in process industries mass-produce large quantities of similar or homogeneous products.
Process firms accumulate production costs by process or by department for a given period of
time
Job – one distinct unit or set of units
Job order costing system – where costs are assigned and accumulated by job
Two ways to measure the costs associated with production
Actual costing – requires the firm to use the actual cost of all direct materials, direct
labour and overhead used in production
oActual cost system
oRarely used because they cannot provide accurate unit cost information on a
timely basis
oMany overhead costs are not incurred uniformly throughout the year
oNonuniform production levels can mean that low production in one month
would give high unit overhead costs
Normal costing – requires firm to assign actual costs of direct materials and direct
labour to units produced and to apply overhead to units based on a predetermined
estimate
oNormal cost system
Normal costing and estimating overhead steps
1. Calculating predetermined overhead rate
Predetermined overhead rate – calculated at the beginning of the year by dividing
the total estimated annual overhead by the total estimated level of associated
activity or cost driver
Overhead rate = estimated annual overhead / estimated annual activity
2. Applying overhead to production
Applied overhead – found by multiplying the predetermined overhead rate by the
actual use of the associated activity for the period
3. Reconciling applied overhead with actual overhead or allocating applied overhead to
WIP and finished goods ending inventories
Underapplied overhead – if actual overhead is greater than applied overhead
oProduct cost has been understated
Overapplied overhead – if actual overhead is less than applied overhead
Plantewide overhead rate – a single overhead rate calculated by using all estimated overhead
for a factory divided by the estimated activity level across the entire factory
Departmental overhead rate – estimated overhead for a department divided by the estimated
activity level for that same department
find more resources at oneclass.com
find more resources at oneclass.com
Document Summary
Acc chapter 5 job order costing. Firms producing unique products or services require a job-order accounting system. Firms in process industries mass-produce large quantities of similar or homogeneous products. Process firms accumulate production costs by process or by department for a given period of time. Job one distinct unit or set of units. Job order costing system where costs are assigned and accumulated by job. Two ways to measure the costs associated with production. Normal costing requires firm to assign actual costs of direct materials and direct labour to units produced and to apply overhead to units based on a predetermined estimate: normal cost system. Normal costing and estimating overhead steps: calculating predetermined overhead rate. Predetermined overhead rate calculated at the beginning of the year by dividing the total estimated annual overhead by the total estimated level of associated activity or cost driver. Overhead rate = estimated annual overhead / estimated annual activity: applying overhead to production.