21642 Chapter Notes - Chapter 10: Indirect Costs, Cost Driver
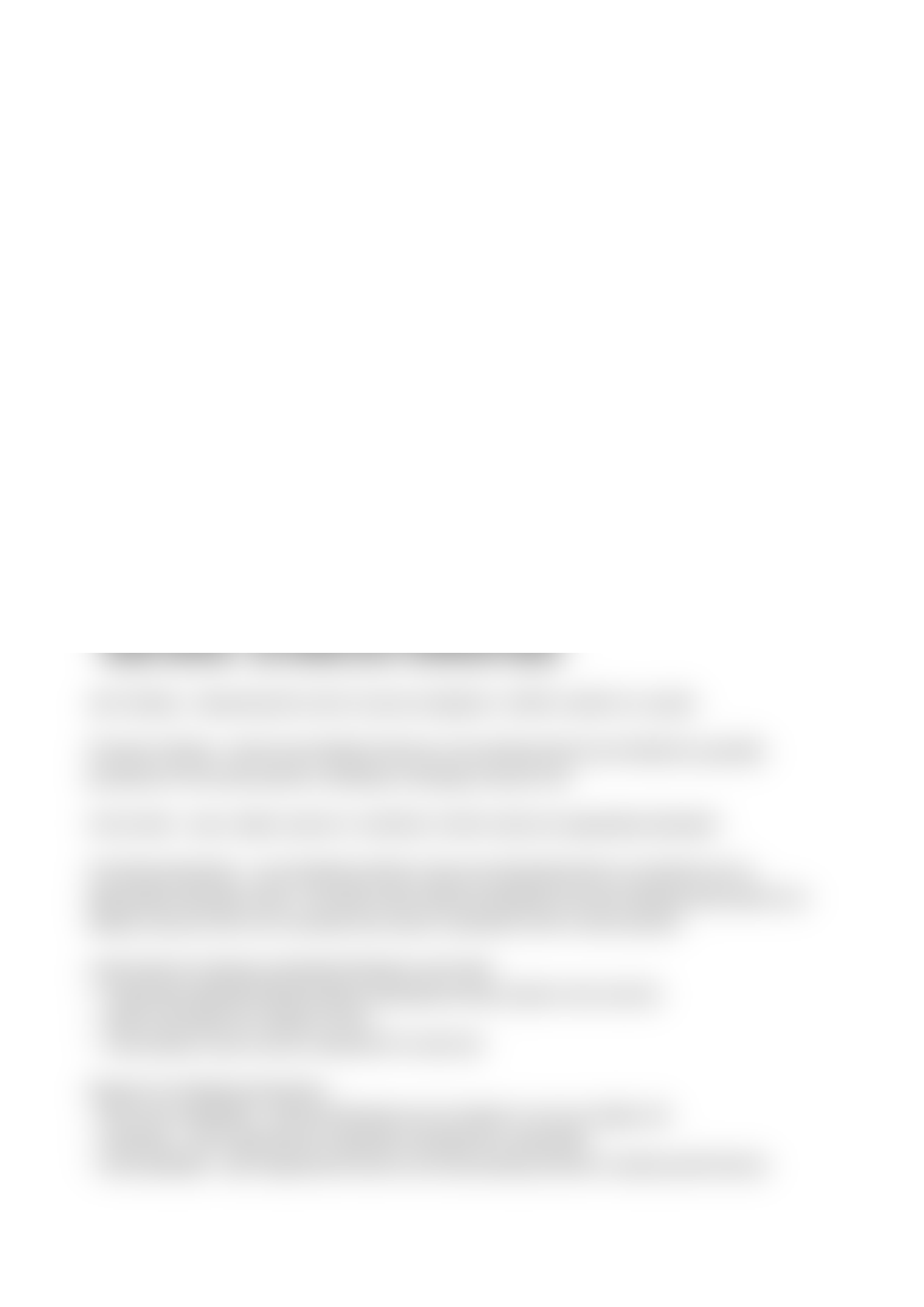
Full Costing
Cost - measurement, in monetary terms, of the amount of resources used for some purpose:
•Cost object - the focus of the costing process
•Direct costs - costs that are traceable directly to the cost objects based on the quantity of the
resource used; two main direct costs are direct materials and direct labour
•Indirect costs (overheads) - costs that cannot be practically traced to the cost objects, allocated
through an allocation base using an overhead allocation method e.g. rent
Cost Concepts:
•Product cost - cost associated with manufacturing a product (DM + DL + OH)
•Period costs - non-product costs that are expensed in the period in which they are incurred eg
marketing
•Full costs - all costs (product and period) associated with the cost object
•Prime costs - includes all direct costs (DL + DM)
•Conversion costs - comprise all product costs for transforming direct materials into finished
goods (OH + DL)
•Selling price - product costs x (1 + markup %)
Absorption full costing an variable costing:
•Absorption cost (full product cost) = direct materials + direct labour + variable overhead +fixed
overhead; part of gross profit (revenues - COGS = gross profit)
•Variable product cost = direct materials + direct labour + variable overhead; part of contrition
margin (revenues - total variable costs = contribution margin)
Job Costing - measuring the cost of a job as singular or within a batch ie a quote.
Process Costing - costs accumulated during an accounting period and divided by quantity
produced for the same period, resulting in average cost per unit.
Cost centre - area, object, person or activity to which costs are separately allocated.
Overhead allocation - accumulating indirect costs and allocating them to products via an
appropriate allocation base. The plant wide method (simplest) involves treating entire plant as a
single cost pool with one overhead rate used to estimate cost for each product.
Logic basis for sharing overheads between cost units:
-Large jobs typically attracts large overheads as they require more service
-Most overheads are related to time
-Direct labour hours can be measured for each job
Reason for dividing businesses:
•Size and complexity - many businesses are too large to run as a single unit
•Expertise - each department is typically managed by a specialist
•Accountability - each department has its own accounting records to assess performance
find more resources at oneclass.com
find more resources at oneclass.com
Document Summary
Job costing - measuring the cost of a job as singular or within a batch ie a quote. Process costing - costs accumulated during an accounting period and divided by quantity produced for the same period, resulting in average cost per unit. Cost centre - area, object, person or activity to which costs are separately allocated. Overhead allocation - accumulating indirect costs and allocating them to products via an appropriate allocation base. The plant wide method (simplest) involves treating entire plant as a single cost pool with one overhead rate used to estimate cost for each product. Logic basis for sharing overheads between cost units: Large jobs typically attracts large overheads as they require more service. Direct labour hours can be measured for each job. Low level of overheads related to direct costs. High level of overheads relative to direct costs.