Engineering Science 1021A/B Lecture Notes - Lecture 15: Fracture, Fracture Mechanics, Stress Intensity Factor
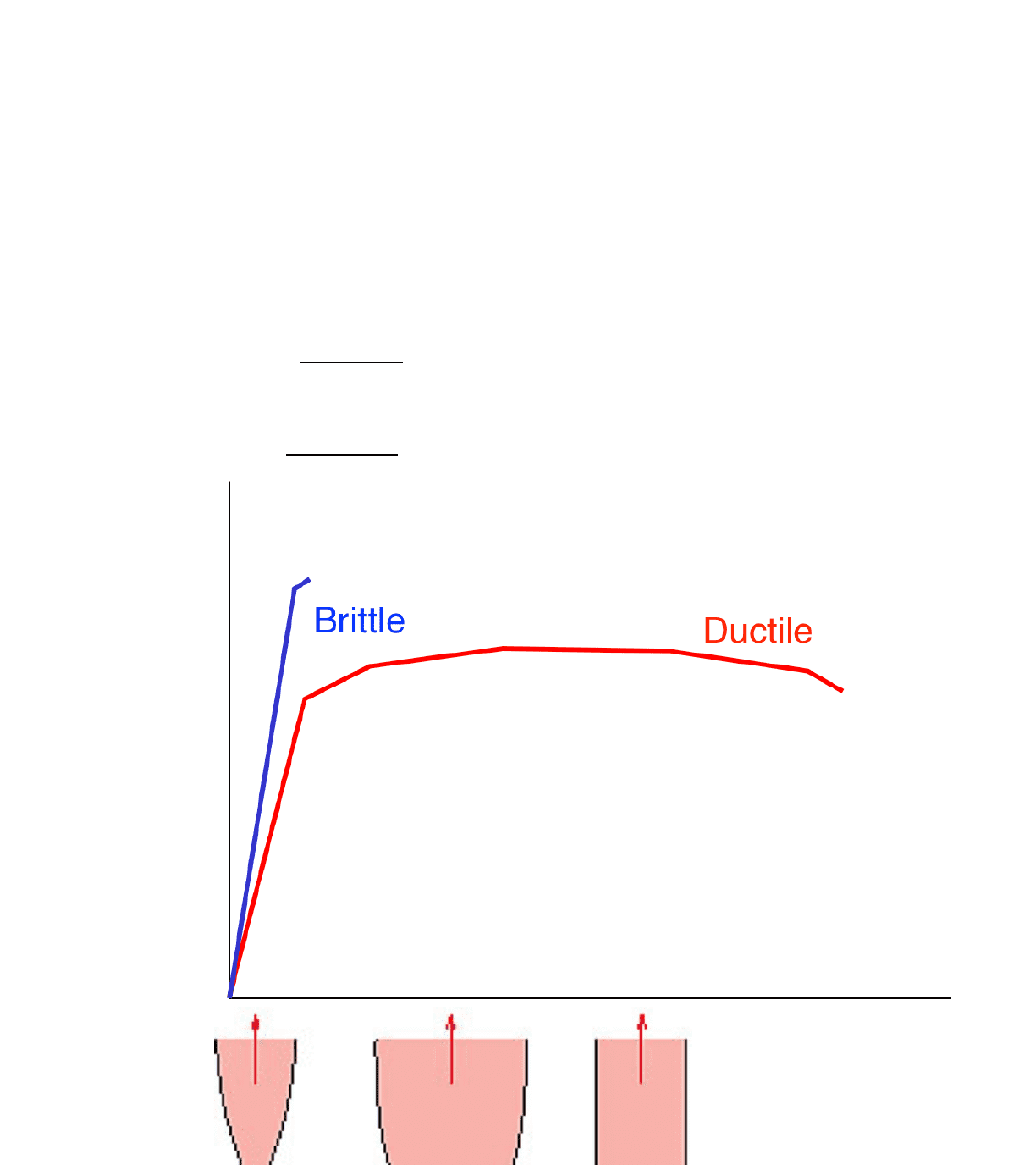
Fracture of any material occurs in 2 steps:
Crack formation
○
Crack propagation
○
•
Failure of engineering materials is classified in terms of being:
Ductile: significant plastic deformation prior to fracture
Requires more energy
§
Preferred because it is slower and provides more warning
§
○
Brittle: little or no plastic deformation
○
○
Highly ductile fracture in which the specimen necks down to a point(a)
Moderately ductile fracture after some necking(b)
Brittle fracture without any plastic deformation(c)
○
•
Ductile Fracture
Results in a "cup and cone" fracture surface in engineering metals
Created by a process known as microvoid coalescence
○
○
•
Spherical dimples characteristic resulting from uniaxial tensile loads(a)
Parabolic-shaped dimples characteristic resulting from uniaxial shear
loading
(b)
•
Stages in the cup-and-cone fracture
Initial necking(a)
Small cavity forming(b)
Coalescence of cavities form a crack(c)
Crack propagation(d)
Final shear fracture at a 45!angle relative to the tensile direction(e)
•
Brittle Fracture
Involves little plastic deformation•
Fracture surface is flat and perpendicular to the applied stress
○
•
A brittle fracture surface often shows:
Chevron markings
§
○
A series of an-like ridges or "river" pattern
○
○
•
Crack propagation in brittle fracture can be either:
Transgranular (cleavage): through the grains
§
○
Intergranular: along the grain boundaries
§
○
In both cases, the surface usually appears shiny because the facets reflect
light
○
•
Stress Concentrations
When a "perfect" solid is loaded in the tension, the normal stress is the same in
any part of the specimen
•
If a flaw (small crack) exists inside a specimen, the free surfaces cannot transmit
any load
The material adjacent to the crack must carry the additional load
○
The stress is concentrated at the edges of the crack
○
•
The degree of concentration of the stress depends on:
The size of the crack (")
○
The radius of the crack tip (#$)
○
○
The geometry of surface/edge and internal cracks(a)
Demonstrating stress amplifications at the crack tip positions (b)
○
•
The stress concentration factor is the ratio of the maximum stress to the
average stress
○
•
Fracture Toughness
A crack will propagate when the stress reaches some critical value•
Stress intensity factor (%): describes behavior of a material that contains a crack
&: geometric factor that depends on crack and specimen size
§
': the average stress
§
": crack size
§
○
•
4 uses of the variable K
Stress concentration factor (%$)
Ratio of the maximum stress to the average stress
§
○
Stress intensity factor (%)
Associated with the geometry of the component
§
○
Critical stress intensity factor (critical Fracture toughness) (%()
The stress intensity factor that will cause a crack to propagate for a
given applied stress
§
Geometry dependant for a given flaw size
§
○
Plain Strain Fracture Toughness (%)()
Material property
§
Minimum value of the fracture toughness for the material
§
Metals: (24-87.4 %)()
Can withstand cracks
the most because
%)(is the highest
•
Ceramics: (0.2-5.0
%)()
Polymers: (0.7-2.2
%)()
○
•
Effect of plate thickness on fracture toughness
○
○
•
Crack Opening Modes
Opening or tensile mode(1)
Sliding mode(2)
Rearing mode(3)
Example 1
An aluminum alloy is subjected to a constant stress of *+,-./0. What is the
maximum tolerable flaw size that will avoid fast fracture? 1%)(23, 456
7-8 '92
3:+-./08 ; 2 *)
Example 2
What is the minimum value of %)(needed to ensure that a plate with a yield
strength of 3,,-./0 and external flaws as large as ,<+-== will plastically
deform before fast fracture can occur when subjected to a tensile load? (; 2
*<*)
The Impact Test
Measures a materials ability to absorb kinetic energy
Toughness: a materials ability to absorb kinetic energy
○
•
The difference in potential energy @ positions 1 and 2 is equal required to
break/deform the specimen
>? 2@ABCDE CFG
§
○
○
•
Impact test data: Energy absorbed & % shear fracture
○
•
The Ductile-to-Brittle Transition
Ductile-to-Brittle Transition Temperature (DBTT): temperature at which the
failure mode of a material changes from ductile to brittle
•
Temperature has a significant influence on the toughness of BCC metals
At low temperatures, they are brittle while at higher temperatures they
more ductile
○
•
•
3 accepted methods of determining the DBTT
*
HIJ
1)
*
HIK
2)
Jfor minimum energy3)
•
•
Fracture
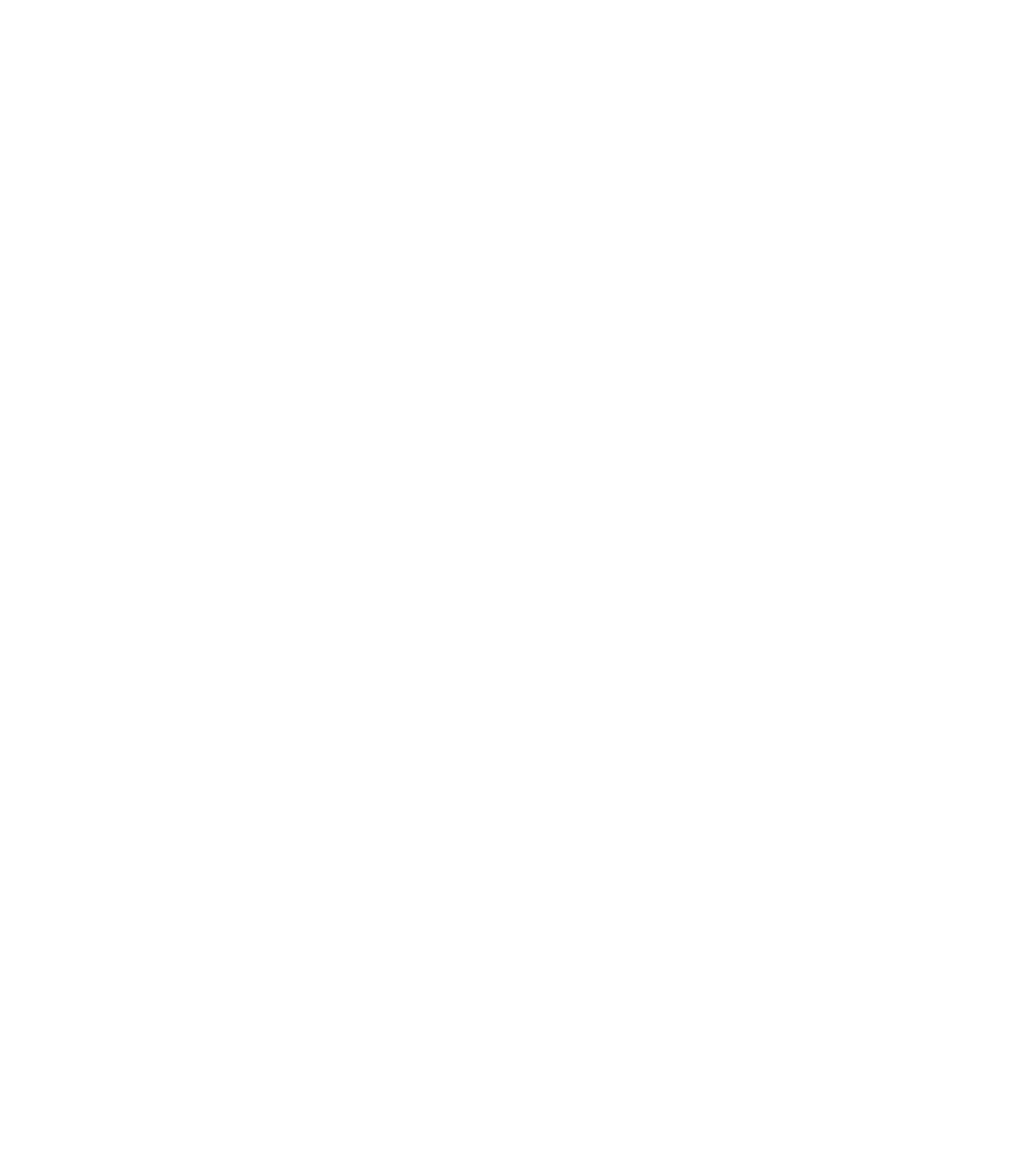
Fracture of any material occurs in 2 steps:
Crack formation
○
Crack propagation
○
•
Failure of engineering materials is classified in terms of being:
Ductile: significant plastic deformation prior to fracture
Requires more energy
§
Preferred because it is slower and provides more warning
§
○
Brittle: little or no plastic deformation
○
○
Highly ductile fracture in which the specimen necks down to a point(a)
Moderately ductile fracture after some necking(b)
Brittle fracture without any plastic deformation(c)
○
•
Ductile Fracture
Results in a "cup and cone" fracture surface in engineering metals
Created by a process known as microvoid coalescence
○
○
•
Spherical dimples characteristic resulting from uniaxial tensile loads(a)
Parabolic-shaped dimples characteristic resulting from uniaxial shear
loading
(b)
•
Stages in the cup-and-cone fracture
Initial necking(a)
Small cavity forming(b)
Coalescence of cavities form a crack(c)
Crack propagation(d)
Final shear fracture at a 45!angle relative to the tensile direction(e)
•
Brittle Fracture
Involves little plastic deformation•
Fracture surface is flat and perpendicular to the applied stress
○
•
A brittle fracture surface often shows:
Chevron markings
§
○
A series of an-like ridges or "river" pattern
○
○
•
Crack propagation in brittle fracture can be either:
Transgranular (cleavage): through the grains
§
○
Intergranular: along the grain boundaries
§
○
In both cases, the surface usually appears shiny because the facets reflect
light
○
•
Stress Concentrations
When a "perfect" solid is loaded in the tension, the normal stress is the same in
any part of the specimen
•
If a flaw (small crack) exists inside a specimen, the free surfaces cannot transmit
any load
The material adjacent to the crack must carry the additional load
○
The stress is concentrated at the edges of the crack
○
•
The degree of concentration of the stress depends on:
The size of the crack (")
○
The radius of the crack tip (#$)
○
○
The geometry of surface/edge and internal cracks(a)
Demonstrating stress amplifications at the crack tip positions (b)
○
•
The stress concentration factor is the ratio of the maximum stress to the
average stress
○
•
Fracture Toughness
A crack will propagate when the stress reaches some critical value•
Stress intensity factor (%): describes behavior of a material that contains a crack
&: geometric factor that depends on crack and specimen size
§
': the average stress
§
": crack size
§
○
•
4 uses of the variable K
Stress concentration factor (%$)
Ratio of the maximum stress to the average stress
§
○
Stress intensity factor (%)
Associated with the geometry of the component
§
○
Critical stress intensity factor (critical Fracture toughness) (%()
The stress intensity factor that will cause a crack to propagate for a
given applied stress
§
Geometry dependant for a given flaw size
§
○
Plain Strain Fracture Toughness (%)()
Material property
§
Minimum value of the fracture toughness for the material
§
Metals: (24-87.4 %)()
Can withstand cracks
the most because
%)(is the highest
•
Ceramics: (0.2-5.0
%)()
Polymers: (0.7-2.2
%)()
○
•
Effect of plate thickness on fracture toughness
○
○
•
Crack Opening Modes
Opening or tensile mode(1)
Sliding mode(2)
Rearing mode(3)
Example 1
An aluminum alloy is subjected to a constant stress of *+,-./0. What is the
maximum tolerable flaw size that will avoid fast fracture? 1%)(23, 456
7-8 '92
3:+-./08 ; 2 *)
Example 2
What is the minimum value of %)(needed to ensure that a plate with a yield
strength of 3,,-./0 and external flaws as large as ,<+-== will plastically
deform before fast fracture can occur when subjected to a tensile load? (; 2
*<*)
The Impact Test
Measures a materials ability to absorb kinetic energy
Toughness: a materials ability to absorb kinetic energy
○
•
The difference in potential energy @ positions 1 and 2 is equal required to
break/deform the specimen
>? 2@ABCDE CFG
§
○
○
•
Impact test data: Energy absorbed & % shear fracture
○
•
The Ductile-to-Brittle Transition
Ductile-to-Brittle Transition Temperature (DBTT): temperature at which the
failure mode of a material changes from ductile to brittle
•
Temperature has a significant influence on the toughness of BCC metals
At low temperatures, they are brittle while at higher temperatures they
more ductile
○
•
•
3 accepted methods of determining the DBTT
*
HIJ
1)
*
HIK
2)
Jfor minimum energy3)
•
•
Fracture
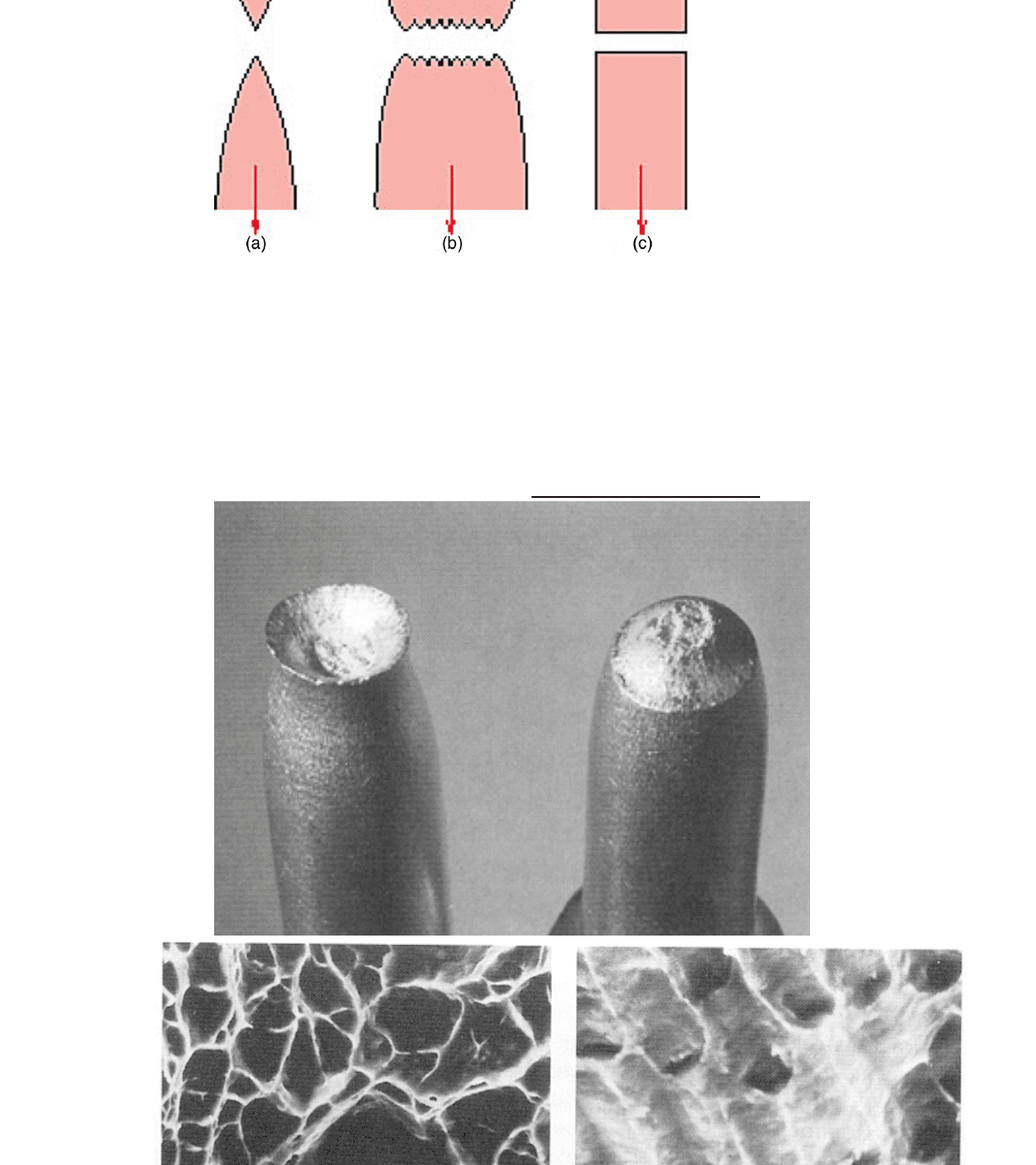
Fracture of any material occurs in 2 steps:
Crack formation
○
Crack propagation
○
•
Failure of engineering materials is classified in terms of being:
Ductile: significant plastic deformation prior to fracture
Requires more energy
§
Preferred because it is slower and provides more warning
§
○
Brittle: little or no plastic deformation
○
○
Highly ductile fracture in which the specimen necks down to a point
(a)
Moderately ductile fracture after some necking
(b)
Brittle fracture without any plastic deformation
(c)
○
•
Ductile Fracture
Results in a "cup and cone" fracture surface in engineering metals
Created by a process known as microvoid coalescence
○
○
•
Spherical dimples characteristic resulting from uniaxial tensile loads(a)
Parabolic-shaped dimples characteristic resulting from uniaxial shear
loading
(b)
•
Stages in the cup-and-cone fracture
Initial necking(a)
Small cavity forming(b)
Coalescence of cavities form a crack(c)
Crack propagation(d)
Final shear fracture at a 45!angle relative to the tensile direction(e)
•
Brittle Fracture
Involves little plastic deformation•
Fracture surface is flat and perpendicular to the applied stress
○
•
A brittle fracture surface often shows:
Chevron markings
§
○
A series of an-like ridges or "river" pattern
○
○
•
Crack propagation in brittle fracture can be either:
Transgranular (cleavage): through the grains
§
○
Intergranular: along the grain boundaries
§
○
In both cases, the surface usually appears shiny because the facets reflect
light
○
•
Stress Concentrations
When a "perfect" solid is loaded in the tension, the normal stress is the same in
any part of the specimen
•
If a flaw (small crack) exists inside a specimen, the free surfaces cannot transmit
any load
The material adjacent to the crack must carry the additional load
○
The stress is concentrated at the edges of the crack
○
•
The degree of concentration of the stress depends on:
The size of the crack (")
○
The radius of the crack tip (#$)
○
○
The geometry of surface/edge and internal cracks(a)
Demonstrating stress amplifications at the crack tip positions (b)
○
•
The stress concentration factor is the ratio of the maximum stress to the
average stress
○
•
Fracture Toughness
A crack will propagate when the stress reaches some critical value•
Stress intensity factor (%): describes behavior of a material that contains a crack
&: geometric factor that depends on crack and specimen size
§
': the average stress
§
": crack size
§
○
•
4 uses of the variable K
Stress concentration factor (%$)
Ratio of the maximum stress to the average stress
§
○
Stress intensity factor (%)
Associated with the geometry of the component
§
○
Critical stress intensity factor (critical Fracture toughness) (%()
The stress intensity factor that will cause a crack to propagate for a
given applied stress
§
Geometry dependant for a given flaw size
§
○
Plain Strain Fracture Toughness (%)()
Material property
§
Minimum value of the fracture toughness for the material
§
Metals: (24-87.4 %)()
Can withstand cracks
the most because
%)(is the highest
•
Ceramics: (0.2-5.0
%)()
Polymers: (0.7-2.2
%)()
○
•
Effect of plate thickness on fracture toughness
○
○
•
Crack Opening Modes
Opening or tensile mode(1)
Sliding mode(2)
Rearing mode(3)
Example 1
An aluminum alloy is subjected to a constant stress of *+,-./0. What is the
maximum tolerable flaw size that will avoid fast fracture? 1%)(23, 456
7-8 '92
3:+-./08 ; 2 *)
Example 2
What is the minimum value of %)(needed to ensure that a plate with a yield
strength of 3,,-./0 and external flaws as large as ,<+-== will plastically
deform before fast fracture can occur when subjected to a tensile load? (; 2
*<*)
The Impact Test
Measures a materials ability to absorb kinetic energy
Toughness: a materials ability to absorb kinetic energy
○
•
The difference in potential energy @ positions 1 and 2 is equal required to
break/deform the specimen
>? 2@ABCDE CFG
§
○
○
•
Impact test data: Energy absorbed & % shear fracture
○
•
The Ductile-to-Brittle Transition
Ductile-to-Brittle Transition Temperature (DBTT): temperature at which the
failure mode of a material changes from ductile to brittle
•
Temperature has a significant influence on the toughness of BCC metals
At low temperatures, they are brittle while at higher temperatures they
more ductile
○
•
•
3 accepted methods of determining the DBTT
*
HIJ
1)
*
HIK
2)
Jfor minimum energy3)
•
•
Fracture