Engineering Science 1021A/B Lecture Notes - Lecture 7: Ultimate Tensile Strength, Modulus Guitars, Ductility
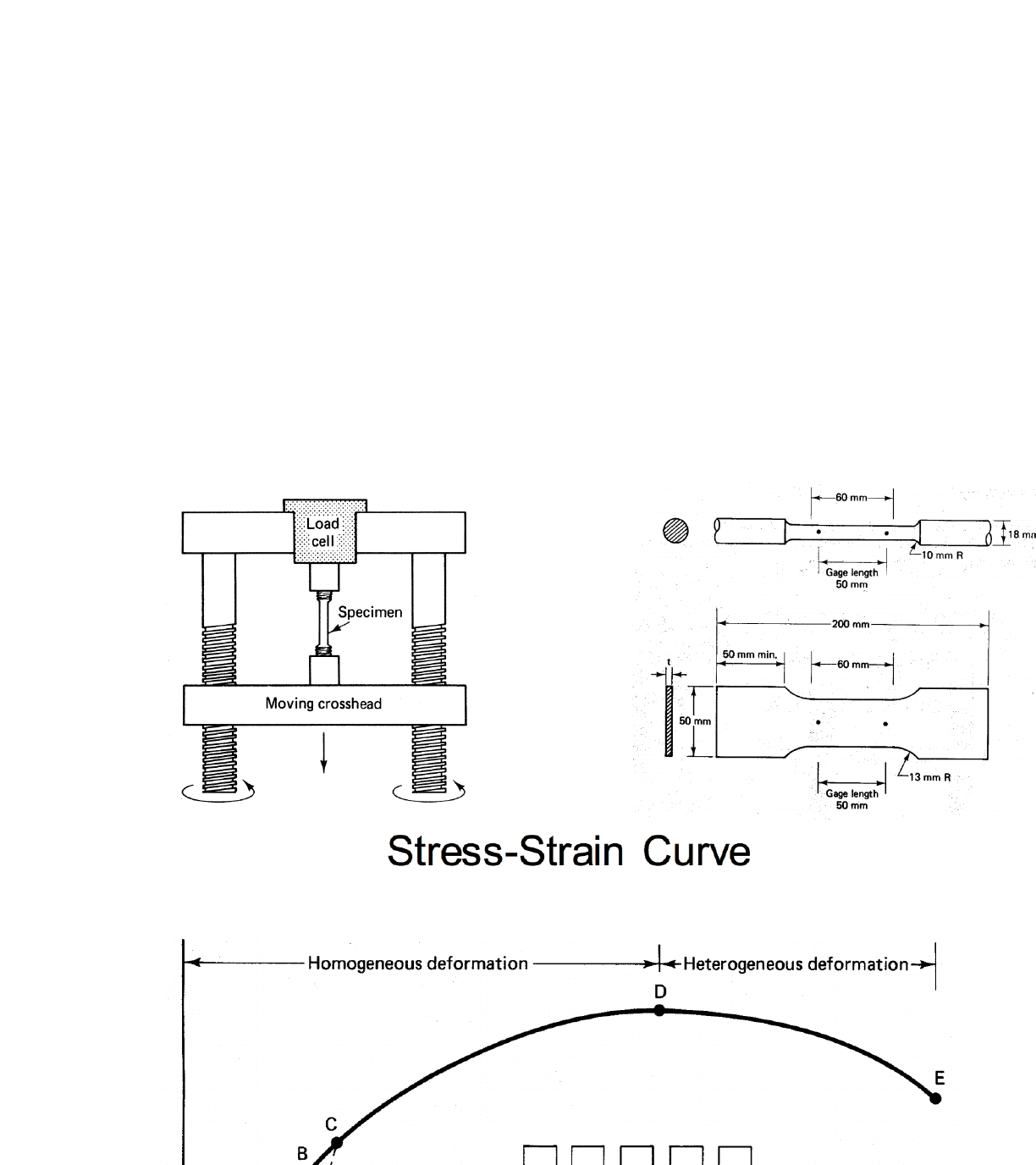
Tensile Test
Stretches a specimen of a prescribed rate and measures the force required
•
Testing machines can be mechanical or hydraulic
•
Specimen geometry:
Reduced gauge section ensures highest stress is away from gripping
mechanism
○
Many standard dimensions to fit various types od materials
○
•
Stretches load until it breaks and measured how much force it takes
•
•
•
Young's Modulus
E will vary according to the bonds in the material:•
High 𝐸Ionic Creamics
Metallic metals
Low 𝐸Covalent/vanderwaal Polymers
•
Yield Strength
As we continue to increase the applied stress, the material eventually “yields”
to the applied stress and exhibits both elastic and plastic deformation
•
The critical stress value needed to initiate plastic deformation is defined as the
yield point of the material
In metallic materials, this is usually the stress required for dislocation
motion, or slip, to be initiated
○
In polymeric materials, this stress will correspond to disentanglement of
polymer molecule chains or sliding of chains past each other
○
•
0.2% Offset Yield
Line parallel to the linear portion of the engineering stress strain curve starting
at
•
this offset value of strain
Offset yield Point: stress value @ intersection of the offset yield line and the
engineering stress strain curve
•
Yield Point Phenomenon
As plastic deformation begins, the stress value drops first from the upper yield
point, then oscillates around an average value defined as the lower yield point
•
For these materials, the yield strength is usually defined from the 0.2% strain
offset
•
The material is expected to plastically deform at the lower yield point•
Tensile Strength
Ultimate Tensile Strength: stress obtained at the highest applied force•
Necking
In ductile materials, deformation does not remain uniform
A region deforms more than others and a large decrease in cross-sectional
area occurs
○
Cross-sectional area becomes smaller at this point, a lower 𝐹is required
to continue its deformation, and the engineering stress, calculated from
the original area decreases
○
•
•
Elastic Properties
Hooke's Law: 𝜎 = 𝐸𝑒•
A steep slope in the Force-distance graph at the equilibrium spacing indicates
high forces are requires to separate the atoms and cause the material to stretch
elastically
•
Binding forces and modulus of elasticity are higher for high-melting point
materials
•
Effect of Temperature
Yield strength, tensile strength, and modulus of elasticity decrease at higher
temperatures, whereas ductility commonly increases
•
Tensile Test
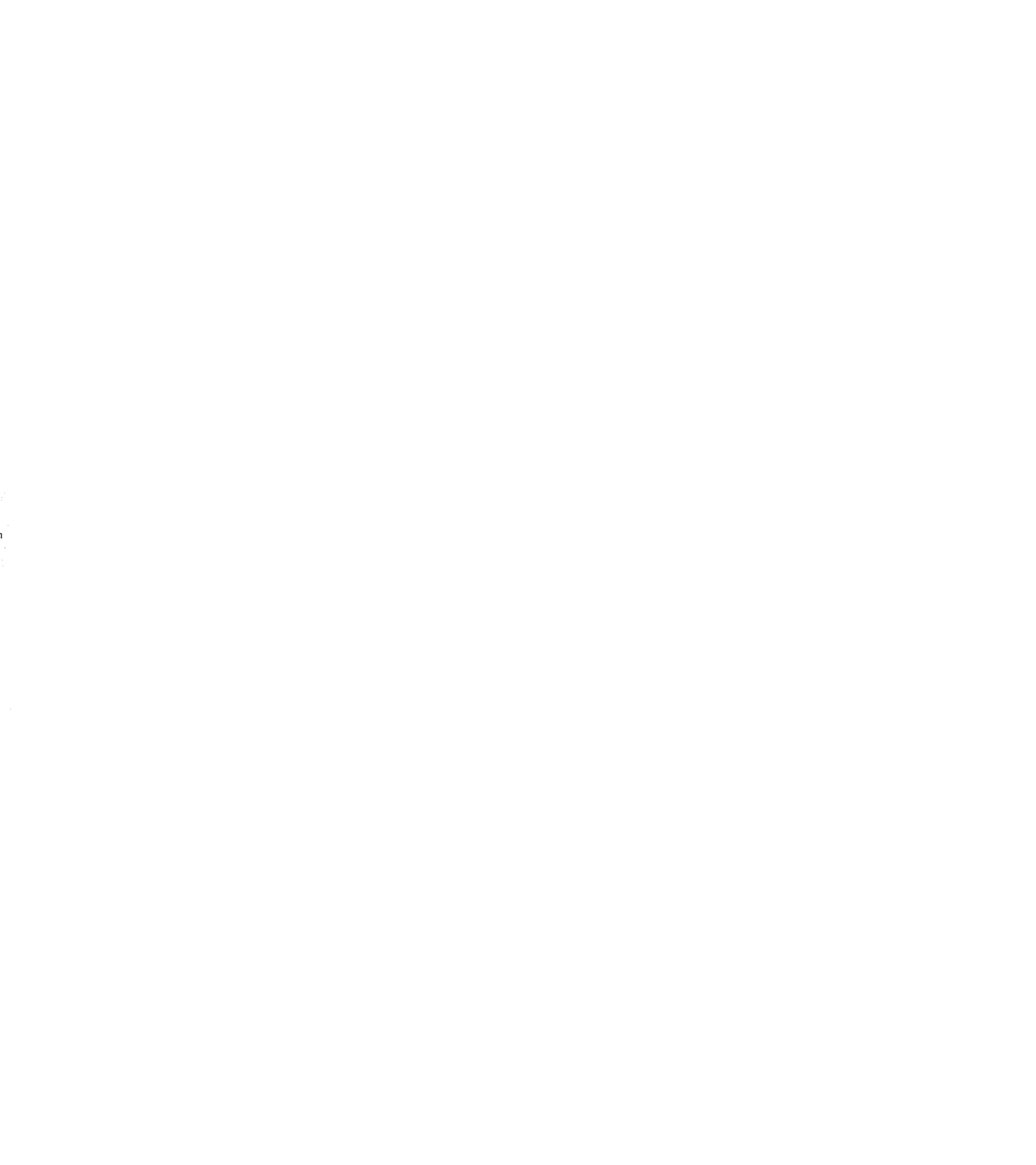
Tensile Test
Stretches a specimen of a prescribed rate and measures the force required•
Testing machines can be mechanical or hydraulic•
Specimen geometry:
Reduced gauge section ensures highest stress is away from gripping
mechanism
○
Many standard dimensions to fit various types od materials
○
•
Stretches load until it breaks and measured how much force it takes•
•
•
Young's Modulus
E will vary according to the bonds in the material:•
High 𝐸Ionic Creamics
Metallic metals
Low 𝐸Covalent/vanderwaal Polymers
•
Yield Strength
As we continue to increase the applied stress, the material eventually “yields”
to the applied stress and exhibits both elastic and plastic deformation
•
The critical stress value needed to initiate plastic deformation is defined as the
yield point of the material
In metallic materials, this is usually the stress required for dislocation
motion, or slip, to be initiated
○
In polymeric materials, this stress will correspond to disentanglement of
polymer molecule chains or sliding of chains past each other
○
•
0.2% Offset Yield
Line parallel to the linear portion of the engineering stress strain curve starting
at
•
this offset value of strain
Offset yield Point: stress value @ intersection of the offset yield line and the
engineering stress strain curve
•
Yield Point Phenomenon
As plastic deformation begins, the stress value drops first from the upper yield
point, then oscillates around an average value defined as the lower yield point
•
For these materials, the yield strength is usually defined from the 0.2% strain
offset
•
The material is expected to plastically deform at the lower yield point•
Tensile Strength
Ultimate Tensile Strength: stress obtained at the highest applied force•
Necking
In ductile materials, deformation does not remain uniform
A region deforms more than others and a large decrease in cross-sectional
area occurs
○
Cross-sectional area becomes smaller at this point, a lower 𝐹is required
to continue its deformation, and the engineering stress, calculated from
the original area decreases
○
•
•
Elastic Properties
Hooke's Law: 𝜎 = 𝐸𝑒•
A steep slope in the Force-distance graph at the equilibrium spacing indicates
high forces are requires to separate the atoms and cause the material to stretch
elastically
•
Binding forces and modulus of elasticity are higher for high-melting point
materials
•
Effect of Temperature
Yield strength, tensile strength, and modulus of elasticity decrease at higher
temperatures, whereas ductility commonly increases
•
Tensile Test
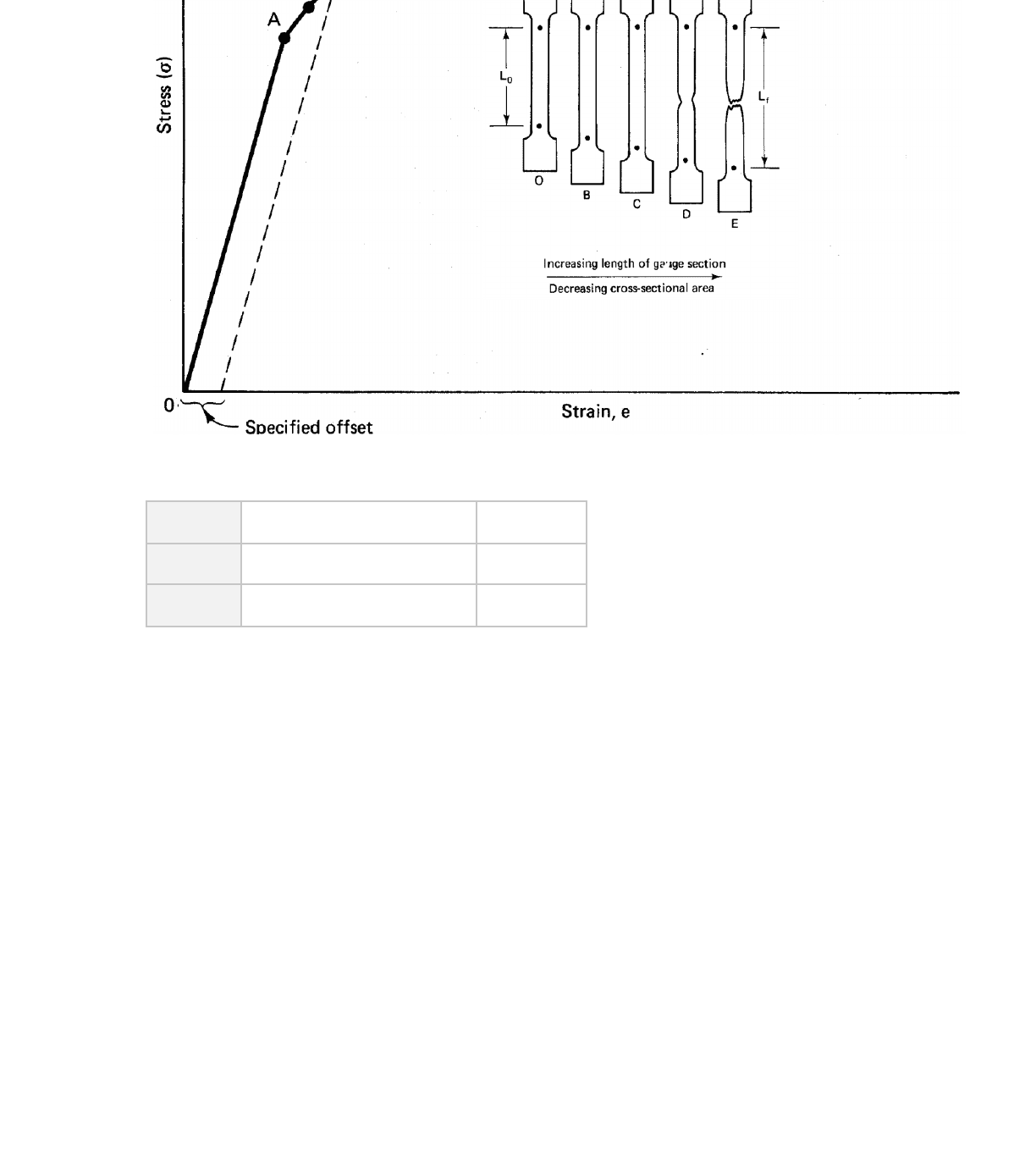
Tensile Test
Stretches a specimen of a prescribed rate and measures the force required•
Testing machines can be mechanical or hydraulic•
Specimen geometry:
Reduced gauge section ensures highest stress is away from gripping
mechanism
○
Many standard dimensions to fit various types od materials
○
•
Stretches load until it breaks and measured how much force it takes•
•
•
Young's Modulus
E will vary according to the bonds in the material:
•
High
𝐸
Ionic
Creamics
Metallic
metals
Low
𝐸
Covalent/vanderwaal
Polymers
•
Yield Strength
As we continue to increase the applied stress, the material eventually “yields”
to the applied stress and exhibits both elastic and plastic deformation
•
The critical stress value needed to initiate plastic deformation is defined as the
yield point of the material
In metallic materials, this is usually the stress required for dislocation
motion, or slip, to be initiated
○
In polymeric materials, this stress will correspond to disentanglement of
polymer molecule chains or sliding of chains past each other
○
•
0.2% Offset Yield
Line parallel to the linear portion of the engineering stress strain curve starting
at
•
this offset value of strain
Offset yield Point: stress value @ intersection of the offset yield line and the
engineering stress strain curve
•
Yield Point Phenomenon
As plastic deformation begins, the stress value drops first from the upper yield
point, then oscillates around an average value defined as the lower yield point
•
For these materials, the yield strength is usually defined from the 0.2% strain
offset
•
The material is expected to plastically deform at the lower yield point•
Tensile Strength
Ultimate Tensile Strength: stress obtained at the highest applied force•
Necking
In ductile materials, deformation does not remain uniform
A region deforms more than others and a large decrease in cross-sectional
area occurs
○
Cross-sectional area becomes smaller at this point, a lower 𝐹is required
to continue its deformation, and the engineering stress, calculated from
the original area decreases
○
•
•
Elastic Properties
Hooke's Law: 𝜎 = 𝐸𝑒•
A steep slope in the Force-distance graph at the equilibrium spacing indicates
high forces are requires to separate the atoms and cause the material to stretch
elastically
•
Binding forces and modulus of elasticity are higher for high-melting point
materials
•
Effect of Temperature
Yield strength, tensile strength, and modulus of elasticity decrease at higher
temperatures, whereas ductility commonly increases
•
Tensile Test
Document Summary
Stretches a specimen of a prescribed rate and measures the force required. Reduced gauge section ensures highest stress is away from gripping mechanism. Many standard dimensions to fit various types od materials. Stretches load until it breaks and measured how much force it takes. E will vary according to the bonds in the material: As we continue to increase the applied stress, the material eventually yields to the applied stress and exhibits both elastic and plastic deformation. The critical stress value needed to initiate plastic deformation is defined as the yield point of the material. In metallic materials, this is usually the stress required for dislocation motion, or slip, to be initiated. In polymeric materials, this stress will correspond to disentanglement of polymer molecule chains or sliding of chains past each other. Line parallel to the linear portion of the engineering stress strain curve starting at this offset value of strain.